What is custom injection moulding and how can it benefit your business?
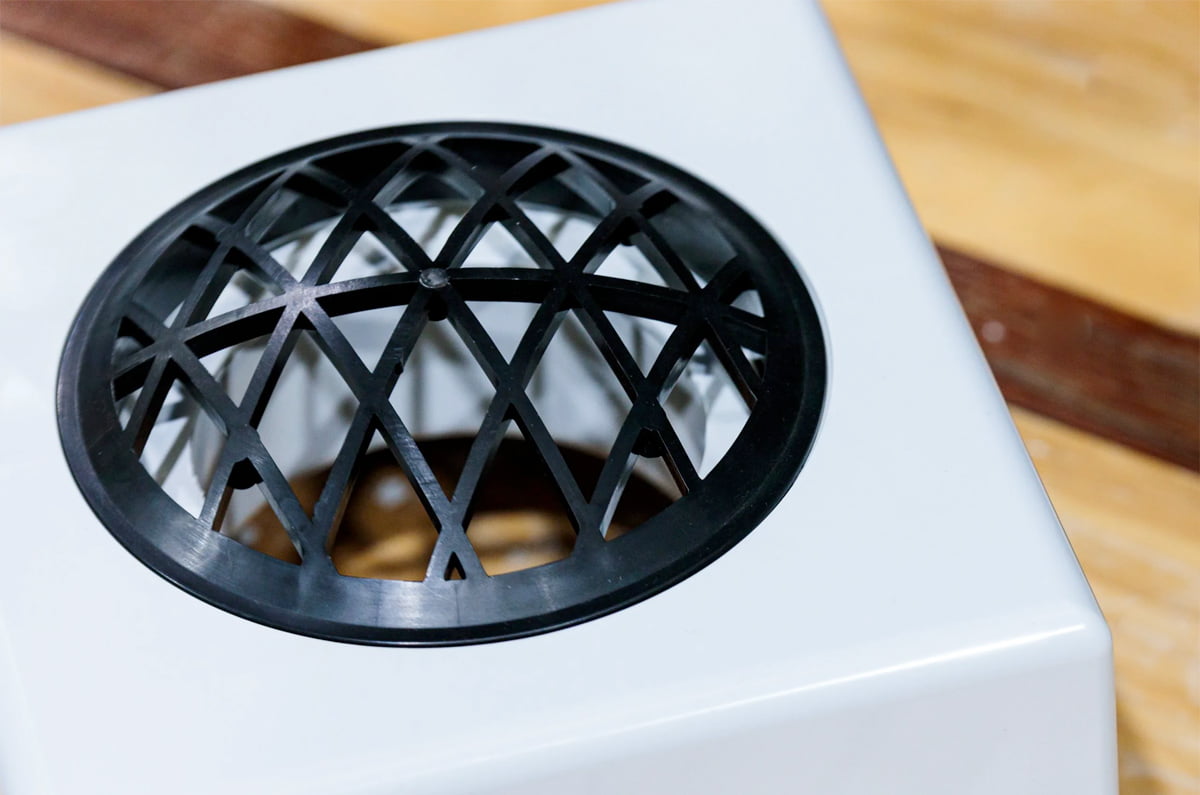
Custom injection moulding is a versatile manufacturing process wherein molten plastic is injected into custom-designed cavities within a mould to create parts tailored to specific requirements. Also known as plastic injection moulding, this method offers a range of advantages for businesses looking to optimise their production processes.
How custom injection moulding works.
The process begins with the injection of molten polymer under pressure into the custom-designed cavity of a die. Once injected, the polymer is cooled and solidified, allowing for the ejection of the part from the die. This method caters to both low-volume and high-volume production runs, ensuring flexibility in meeting varying demands.
Benefits of Custom Injection Moulding
Strength and Durability: With proper mould/part design and material selection, plastic injection moulding delivers parts that rival the strength of steel, ensuring durability and longevity.
Cost-Effectiveness: Minimal labour requirements make plastic injection moulding a highly cost-effective solution. Efficiency in the manufacturing process translates to savings for both manufacturers and customers.
Scalability: Custom injection moulding enables the production of large quantities of parts efficiently, accommodating the needs of diverse projects.
Versatility in Design: The method offers flexibility in shaping parts of any size or complexity, allowing for intricate designs and tailored solutions.
Detail and Precision: High-pressure manufacturing facilitates detailed and intricate designs within products, enhancing their functionality and aesthetic appeal.
Fast Turnaround: Multi-cavity moulds enable faster production, ensuring timely delivery of parts to meet project deadlines.
Material Flexibility: A wide range of resins allows for the selection of materials with properties suited to specific applications, enhancing product performance and longevity.
Colour Customisation: Plastic injection moulding offers extensive colour options, enabling seamless integration with existing structures or surroundings.
Why Choose Plastic Injection Moulding?
Plastic injection moulding stands out as the preferred method for manufacturing plastic parts due to its numerous advantages:
Complexity: The process allows for the creation of intricate components with minimal waste and high uniformity.
Efficiency: Fast cycle times and minimal manufacturing problems ensure efficient production.
Cost-Effectiveness: Low labour costs make plastic injection moulding a financially viable option.
Precision and Consistency: The method ensures high precision and consistency across thousands of components, reducing defect percentages.
Lightweighting: Weight reduction without compromising strength or flexibility is achievable, meeting diverse industry requirements.
Flexibility: Endless possibilities in material combinations and characteristics cater to varied application needs.
For cost-effective sewerage or stormwater solutions tailored to your civil engineering projects, Beaufox Industries is your trusted partner. Find out more here www.beaufox.com.au